It is possible to classify mechanical seals in several ways. However, here we are going to classify them based on the basic criterion; balanced type mechanical seals and unbalanced mechanical seals.
There are three different types of mechanical seals which are commonly used in the process: Cartridge, Component, Air
Before we classify, let’s understand the term ‘Mechanical Seal Balance’.
It is nothing but the load that acts across the seal face. If the load is quite high, then the liquid film between the rings of the seal gets vaporized. Sometimes, it gets squeezed out.
Due to the thermoelastic instability and unstable condition, there could be heavy wear and tear on the sealing surfaces.
A well-balanced seal avoids all these problems. It lasts longer and works more efficiently.
The pressure acts equally in all directions. It forces the primary ring against the mating ring and keeps them in place. The force is called closing force.
When there is a need for reducing the force, the diameter of the sleeve shoulder is decreased. Alternatively, the diameter of the seal hardware can also be reduced. It is called seal balancing.
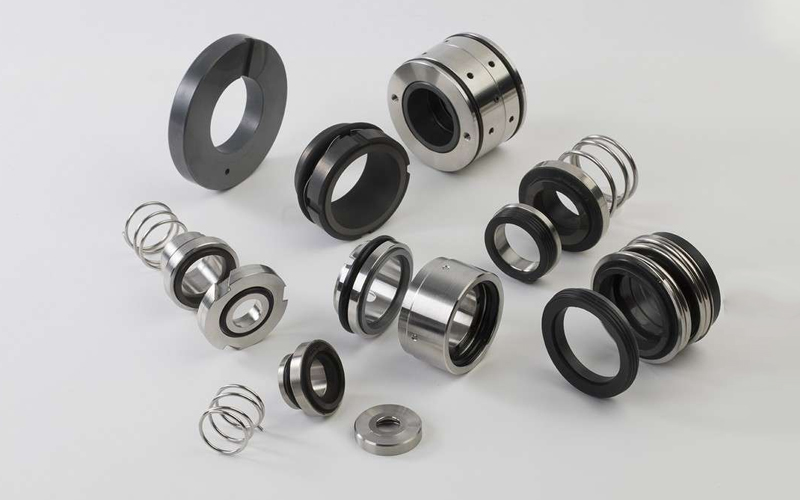
UNBALANCED SEALS
When the stuffing box pressure is greater than the average pressure between the seal faces, it is known as an unbalanced seal.
In this case, the seals exhibit net hydraulic closing force generated by the actual pressure to be sealed.
Experts say that the unbalanced seals are more stable than balanced seals as far as misalignment, cavitation, and vibration is concerned.
However, these seals have a relatively low-pressure limit. When the closing force exerted is more than the pressure limit, the lubricating film comes out.
It results in greatly loaded dry running seal failure.
BALANCED SEALS
In balanced seal, the opening area or face area is same as an unbalanced seal. However, here the closing area is reduced.
Since the force exerted is equal to pressure times area, it gets reduced here.
In simple words, to make a seal balanced, a small design change is required. It reduces the hydraulic force that closes the seal faces.Therefore, balanced seals run more smoothly than unbalanced seals and last long. The pressure limits of the balanced seal are high. They generate less heat than others.
Liquids of low lubricity can be handled better by balanced seals.
Both balanced and unbalanced seals have merits and demerits. It depends on the specific application which one is more suitable.
There are several basic designs available. To choose the most suitable designs amongst all, engineers study the requirement specs thoroughly.